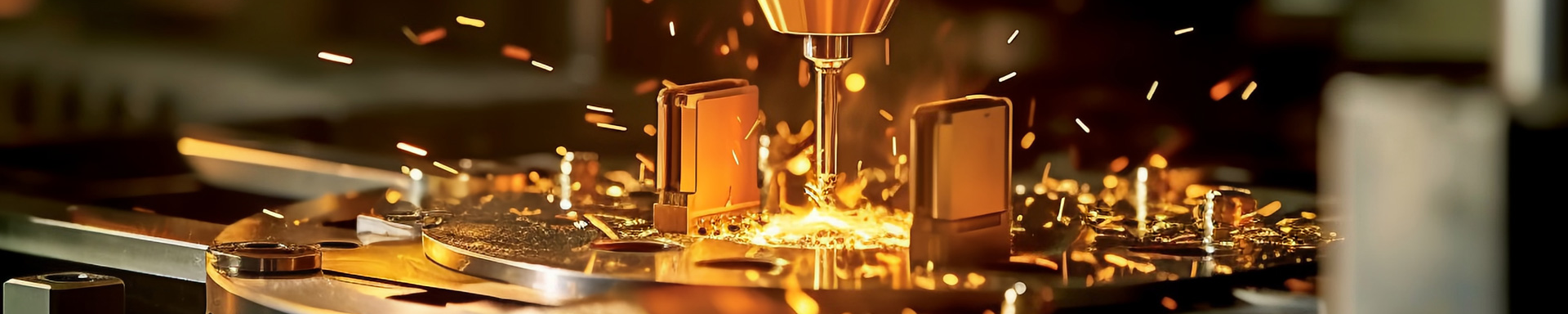
Técnicas avançadas em processos de fundição sob pressão de automóveis
2024-11-22 15:41Melhorias na fundição sob pressão de alta pressão (HPDC)
A fundição sob pressão de alta pressão (HPDC) continua sendo uma pedra angular da produção de componentes automotivos, valorizada por sua velocidade e capacidade de criar peças complexas. No entanto, a HPDC tradicional frequentemente luta para atingir precisão dimensional consistente e qualidade de superfície em grandes lotes. Os aprimoramentos modernos se concentram na otimização de todo o processo, desde o design da matriz e seleção de material até parâmetros de injeção e técnicas de pós-processamento. Isso inclui avanços em materiais de matriz que oferecem resistência superior ao desgaste e propriedades de transferência de calor, levando à vida útil estendida da matriz e à qualidade aprimorada da peça. Além disso, a implementação de sistemas de controle sofisticados permite o monitoramento e o ajuste precisos de parâmetros como pressão de injeção, velocidade e tempo de espera, minimizando variações e garantindo resultados consistentes.
Outra área crítica de melhoria é o uso de software de simulação. Esses programas avançados permitem que os engenheiros testem virtualmente vários projetos de matriz e parâmetros de injeção antes que a produção real comece. Essa capacidade preditiva reduz significativamente a necessidade de prototipagem física e iterações dispendiosas, acelerando o processo de desenvolvimento e minimizando o desperdício. A integração de sensores sofisticados dentro da máquina de fundição fornece feedback em tempo real, aprimorando ainda mais o controle do processo e otimizando o resultado. Essa abordagem orientada por dados leva a melhorias significativas na qualidade da peça, reduzindo defeitos e aumentando a eficiência geral.
Fundição sob pressão de parede fina
A demanda por veículos leves está impulsionando um forte impulso em direção à fundição sob pressão de parede fina. Essa técnica permite a criação de componentes com espessuras de parede significativamente reduzidas, mantendo a integridade estrutural. Isso não apenas contribui para a redução de peso, mas também reduz os custos de material. No entanto, obter fundição de parede fina requer controle preciso sobre o processo de injeção e o uso de matrizes especializadas. Técnicas avançadas empregam projetos de matriz otimizados com sistemas de resfriamento aprimorados para garantir a solidificação rápida e evitar defeitos como porosidade ou empenamento. O desenvolvimento de ligas de alumínio de alta resistência, especificamente adequadas para aplicações de parede fina, aumenta ainda mais a viabilidade e a resistência desses componentes.
O processo também se beneficia de inovações no design de matrizes, incorporando recursos como sistemas de gating otimizados e estratégias de ventilação para melhorar o fluxo de metal e minimizar o aprisionamento de ar. Simulações avançadas desempenham um papel crucial na previsão de problemas potenciais e na otimização dos parâmetros do processo para atingir a geometria de parede fina desejada, mantendo a integridade estrutural e a qualidade da superfície. A implementação de sistemas de monitoramento e controle em tempo real minimiza ainda mais os defeitos e garante a produção consistente de componentes de alta qualidade.
Fundição sob pressão multimaterial
A integração de vários materiais em um único componente de fundição sob pressão abre possibilidades interessantes para melhorar a funcionalidade e o desempenho. Essa abordagem permite a combinação de materiais com propriedades diferentes, como resistência, condutividade térmica e condutividade elétrica, em uma única peça. Por exemplo, um componente pode incorporar um núcleo de liga de alumínio de alta resistência para integridade estrutural, combinado com um material mais macio e dúctil em áreas específicas para melhorar a funcionalidade ou reduzir o desgaste. Isso requer um design de matriz sofisticado e controle preciso sobre o processo de injeção para garantir o posicionamento e a colagem precisos dos diferentes materiais.
Técnicas avançadas em fundição sob pressão multimaterial geralmente envolvem o uso de insertos especializados dentro da matriz para definir os limites de diferentes materiais. O controle preciso sobre os parâmetros de injeção é crucial para evitar a mistura ou delaminação dos diferentes materiais. O uso de software de simulação é particularmente crítico na otimização dos parâmetros de projeto e processo, garantindo a integração e a colagem bem-sucedidas de vários materiais dentro do componente final. O desenvolvimento de novas técnicas de junção, como soldagem por fricção ou colagem por difusão, também está desempenhando um papel importante na criação de fundições multimateriais robustas e confiáveis.
Materiais e revestimentos avançados para matrizes
O desempenho e a longevidade das matrizes de fundição sob pressão impactam significativamente a eficiência geral e a qualidade do processo. Os materiais tradicionais de matriz, embora funcionais, frequentemente apresentam limitações em termos de resistência ao desgaste, condutividade térmica e resistência à corrosão. Os avanços modernos se concentram no desenvolvimento e na aplicação de materiais inovadores de matriz, como ligas de aço avançadas, compósitos cerâmicos e novos revestimentos. Esses materiais fornecem maior durabilidade, permitindo maiores taxas de produção e maior vida útil da matriz.
Revestimentos especializados, aplicados à superfície da matriz, aumentam ainda mais a resistência ao desgaste, reduzem o atrito e melhoram o acabamento da superfície dos componentes fundidos. Esses revestimentos podem ser adaptados para aplicações específicas, oferecendo propriedades personalizadas, como transferência de calor aprimorada ou características de liberação. O desenvolvimento de revestimentos mais duráveis e confiáveis está em andamento, com foco em atingir uma resistência ao desgaste ainda maior e melhorar a qualidade geral das peças fundidas. Isso permite maiores taxas de produção e melhor qualidade dos componentes, ao mesmo tempo em que minimiza o tempo de inatividade associado à manutenção e substituição da matriz.